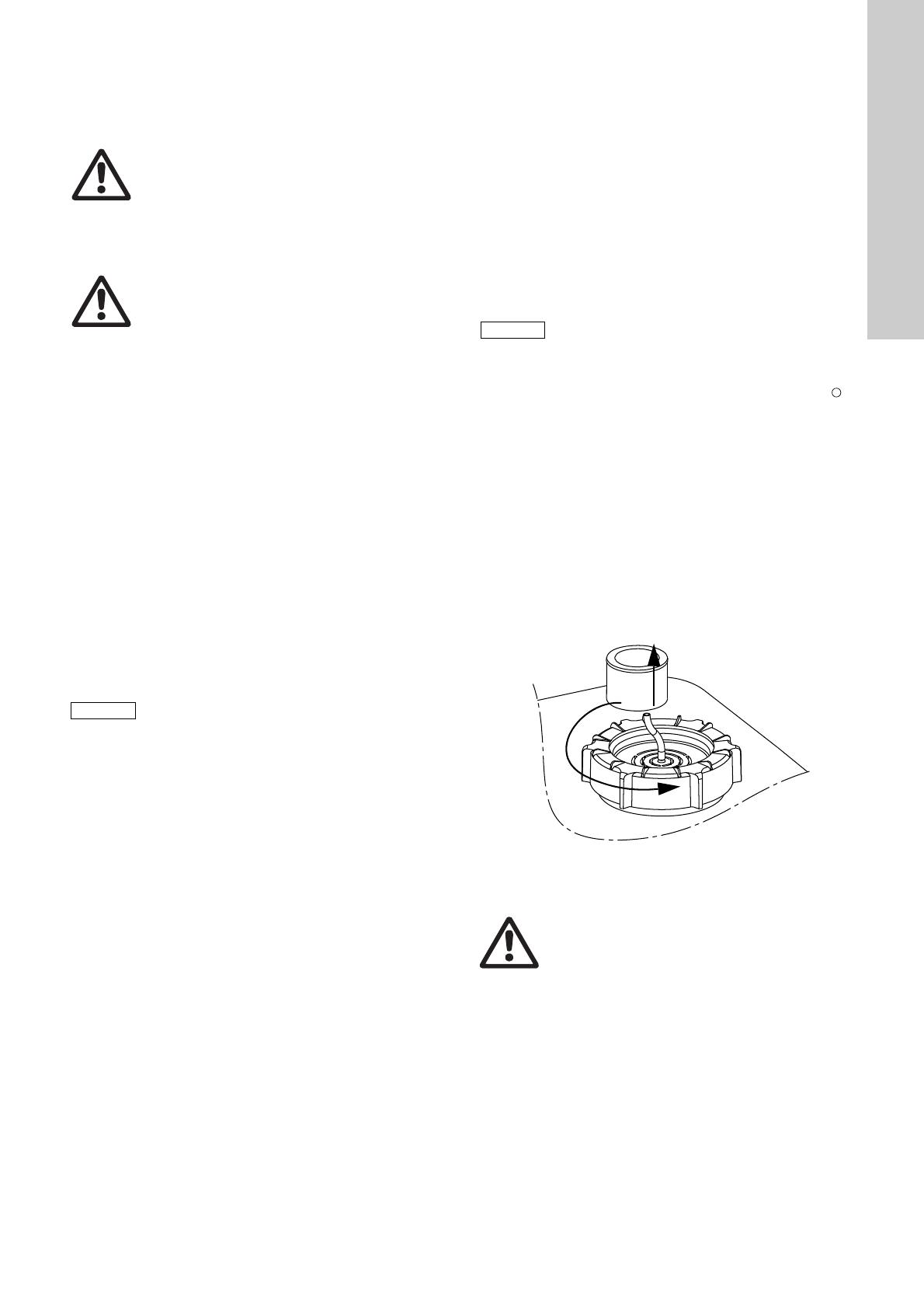
English (GB)
17
9. Maintenance and service
The Multilift MSS requires a minimum of maintenance.
According to EN 12056-4, lifting stations in single-family houses
must be checked once a year. During the check, local regulations
must be observed.
The periodic checks of the lifting station must be carried out by
authorised personnel and must comprise electrical and
mechanical maintenance.
Check the following points:
• Outlet and inlet connections
Check all connections to the lifting station for tightness and
leakages. Make sure that weight from the inlet, outlet and
venting pipes does not rest on the tank. Long pipe sections,
valves, etc. must be supported.
• Power consumption
See nameplate.
• Cable entry
Make sure that the cable entry is watertight and that the
cables are not bent sharply and/or pinched.
• Pump parts
Check that the vent hole of the pump housing is clear by
dismantling the pump from the support flange.
We recommend replacing the O-ring sealing between pump
and support flange.
Make a test run with clean water. In case of noise, vibration or
abnormal running, contact Grundfos.
• Shaft seal
Check the shaft seal, O-ring and oil. The oil chamber contains
60 ml non-poisonous oil. Used oil must be disposed of in
accordance with local regulations. This work must be carried
out by the manufacturer or an authorised service workshop.
See service instructions.
Cleaning the non-return valve (if required)
Proceed as follows:
1. Close the isolating valves in the outlet pipe and in the inlet
pipe (if fitted) or drain the outlet pipe by tightening the drain
screw on the side of the non-return valve.
See section 5.1.3 Non-return valve.
2. Clean the non-return valve via its inspection cover.
Replace the gasket of the inspection cover when
reassembling the non-return valve.
9.1 Electrical maintenance
• Check the gaskets of the LC 220 cabinet front cover and of the
cable entries.
• Check the cable connections.
• Check the controller functions.
• Check and clean the pressure tube. See section 9.2 Cleaning
the level sensor.
• If LC 220 is installed in a particularly moist environment in a
basement, we recommend checking the terminals on the PCB
in order to identify possible corrosion. In typical installations,
the contacts will work for many years and do not require any
inspection.
• Replace the 9 V battery, if fitted, in connection with annual
service.
9.2 Cleaning the level sensor
1. Push the ON-OFF-AUTO selector switch to position OFF ( ).
See section 5.2.2 Control elements and indicator lights.
2. Loosen the screw cap by turning it counterclockwise.
See fig. 19.
3. Lift the pressure tube carefully out of the collecting tank.
Do not lift it by means of the hose.
4. Check for possible deposits on or in the pressure tube. See
section 5.1.4 Level sensor.
5. Scrape off any deposits. If necessary, remove the hose from
the controller and rinse the tube and hose with clean water at
low pressure. Make sure no water remains in the hose.
6. Refit the pressure tube by screwing the screw cap on to the
tank. Reconnect the hose to the controller.
7. Check the sensor by test running Multilift MSS.
Fig. 19 Removing the pressure tube
9.3 Contaminated lifting station or components
If Grundfos is requested to service the lifting station, Grundfos
must be contacted with details about the pumped liquid, etc.
before the lifting station is returned for service. Otherwise
Grundfos can refuse to accept the lifting station for service.
Lifting stations which have been in contact with the pumped liquid
must be thoroughly cleaned before they are returned to Grundfos.
Any costs of returning the lifting station are to be paid by the
customer.
However, any application for service (no matter to whom it may
be made) must include details about the pumped liquid if the
lifting station has been used for liquids which are injurious to
health or toxic.
Warning
Before carrying out maintenance and service on
lifting stations used for pumping liquids which might
be hazardous to health, make sure that the lifting
station has been thoroughly flushed with clean water
and that the outlet pipe has been drained. Rinse the
parts in water after dismantling. Make sure that the
isolating valves have been closed. The work must be
carried out in accordance with local regulations.
Warning
Before making any connections in LC 220 or working
on lifting stations, make sure that the power supply
has been switched off and that it cannot be
accidentally switched on.
Do not loosen the support flange. It is screwed and
sealed to the collecting tank. Loosen the four
stainless steel clamps instead.
The above list is not complete. LC 220 may be
installed in environments which require thorough and
frequent maintenance.
TM05 0545 1011
Warning
If a Multilift lifting station has been used for a liquid
which is injurious to health or toxic, it will be
classified as contaminated.