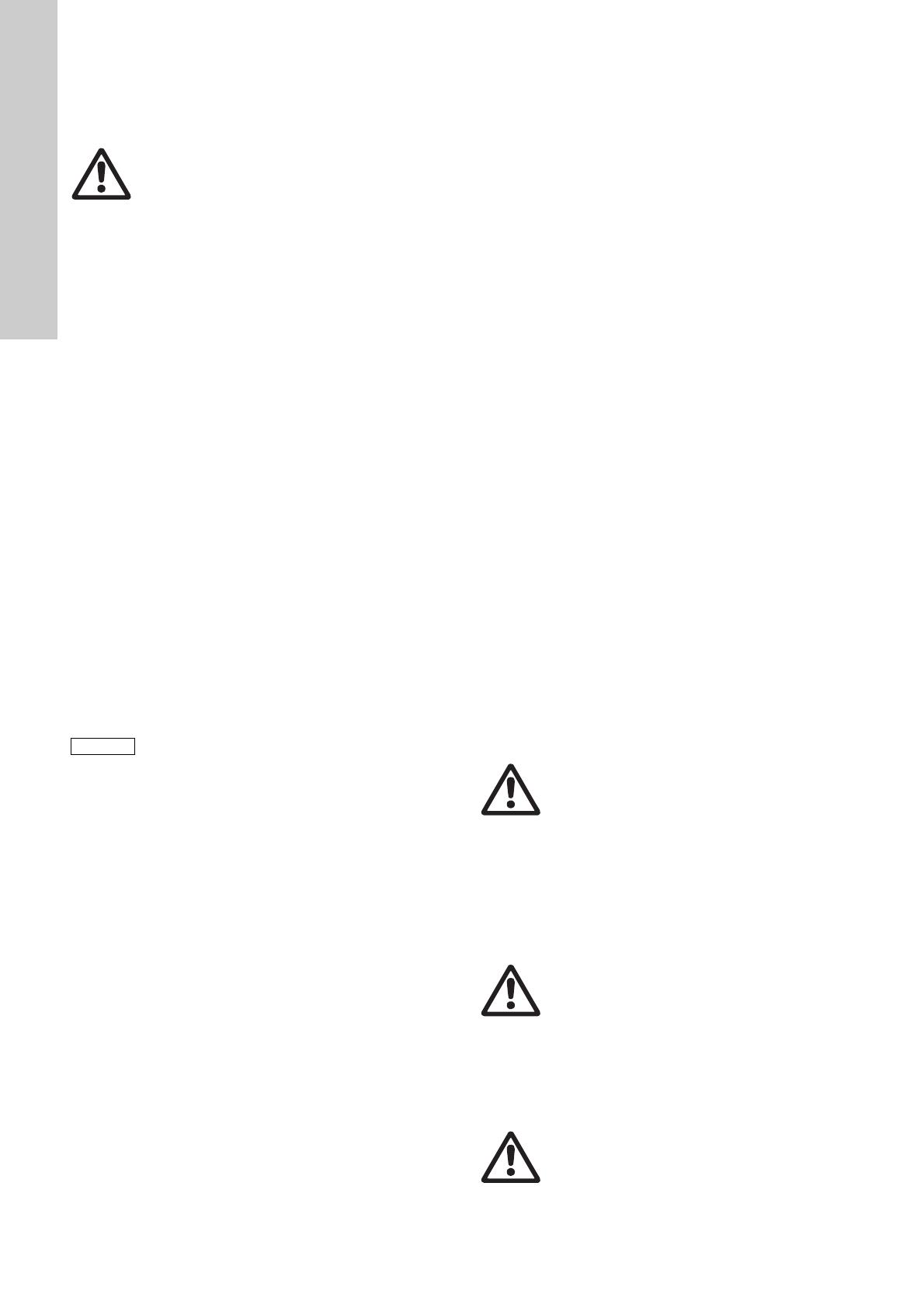
English (GB)
6
2.2 Safety advice for handling chlorine
2.2.1 Risks to health
Chlorine gas is toxic, more than 50 Vol.-ppm in the indoor air
mean an acute danger to life.
Hazards of chlorine gas
• Irritating to eyes, respiratory system and skin.
• Causes whooping cough.
• Causes causticization of skin and respiratory system.
• Lethal by lung edema in case of long influence or high
concentration.
• Slight paralyzing effect to the central nervous system.
Hazards of liquid chlorine
• Causes causticization of skin.
• Causes reddening and formation of bubbles.
2.2.2 Personal safety equipment
The operating authority of a chlorination plant has to provide for
the operation personnel:
For each person
Respiratory equipment (full-sight gas mask)
• with an effective chlorine filter (B2P3), colour mark: grey with a
white ring
• at least 1 spare filter per gas mask
• personally fitted (perfectly tight)
• labelled by name
Only plants with chlorine drums
• at least 2 protective suits with compressed air respirators
Storage of the safety equipment
• outside the chlorine rooms
• well visible
• easily available at any time
• protected from dust and moisture
• Introducing the operation personnel to handle the safety
equipment
• Carrying out exercises (at least half-yearly)
• Regular replacement of the gas mask filters
– after the expiry of the date of durability
– at least 6 months after opening (mark the opening date on
the filter)
– after contact with chlorine
– Observe employing prohibition according to § 14 ArbStoffV
(in Germany) resp. according to local laws!
2.2.3 Rules of conduct
• Change of chlorine containers only with gas mask.
• Entering contaminated rooms only with protective suit and
compressed air respirator.
• In case of flight wear gas mask, if possible.
Observe wind direction!
• Eating, drinking and storing food is prohibited in chlorine
rooms.
2.2.4 First aid in case of accidents
First aid after having inhalated chlorine
• Keep calm.
• Remove injured persons from the dangerous area.
– Helpers must pay attention to personal protection!
• Immediately remove contaminated clothes.
• Calm down injured persons and keep them warm with
blankets.
• Supply fresh air; use oxygen respirator (alternately with
inhalating steam), if possible.
– No mouth-to-mouth resuscitation!
• Fast and gentle transport to hospital
– lying
– sitting in case of difficulty in breathing
– state chlorine causticization as the cause.
First aid after causticization of the skin
• Keep calm.
• Remove contaminated clothes.
• Rinse skin with plenty of water
• Bandage the wound germ-freely
• Seek medical aid.
– State chlorine causticization as the cause.
First aid after causticization of the eyes
• Keep calm.
• Rinse causticized eyes with plenty of water while the person is
lying.
– Protect healthy eye, if necessary.
– Spread eyelids widely, let the eye move to all sides.
• Seek ophthalmologist.
– State chlorine causticization as the cause.
First aid after internal causticization
• Keep calm.
• Drink water in short sips.
– If possible, take medical charcoal.
• Seek medical aid.
– state chlorine causticization as the cause.
2.2.5 Transport and storage of chlorine
Basic rules for transport and storage of chlorine
• Treat containers carefully, do not throw!
• Protect containers from turning over or rolling away!
• Protect containers from direct sun rays and temperatures over
50 °C!
• Transport of containers only with valve protection nut and
protection cap.
Valid regulations
– Regulations for accident prevention "Chlorination of water"
(GUV-V D5) with process instructions
– Regulations concerning places of work (ArbStättV)
– Technical rules for gases 280, 310 und 330
Warning
R 23 Toxic by inhalation.
R 36/37/38 Irritating to eyes, respiratory system
and skin.
Further obligations of the operating authority
Warning
Handling of chlorine containers only by experienced,
practised personnel!
Warning
This rules are valid for both full and empty
containers, as empty containers still contain rests of
chlorine and therefore are under pressure.
Warning
Strictly observe local law and regulations for
handling, transport and storage of chlorine.