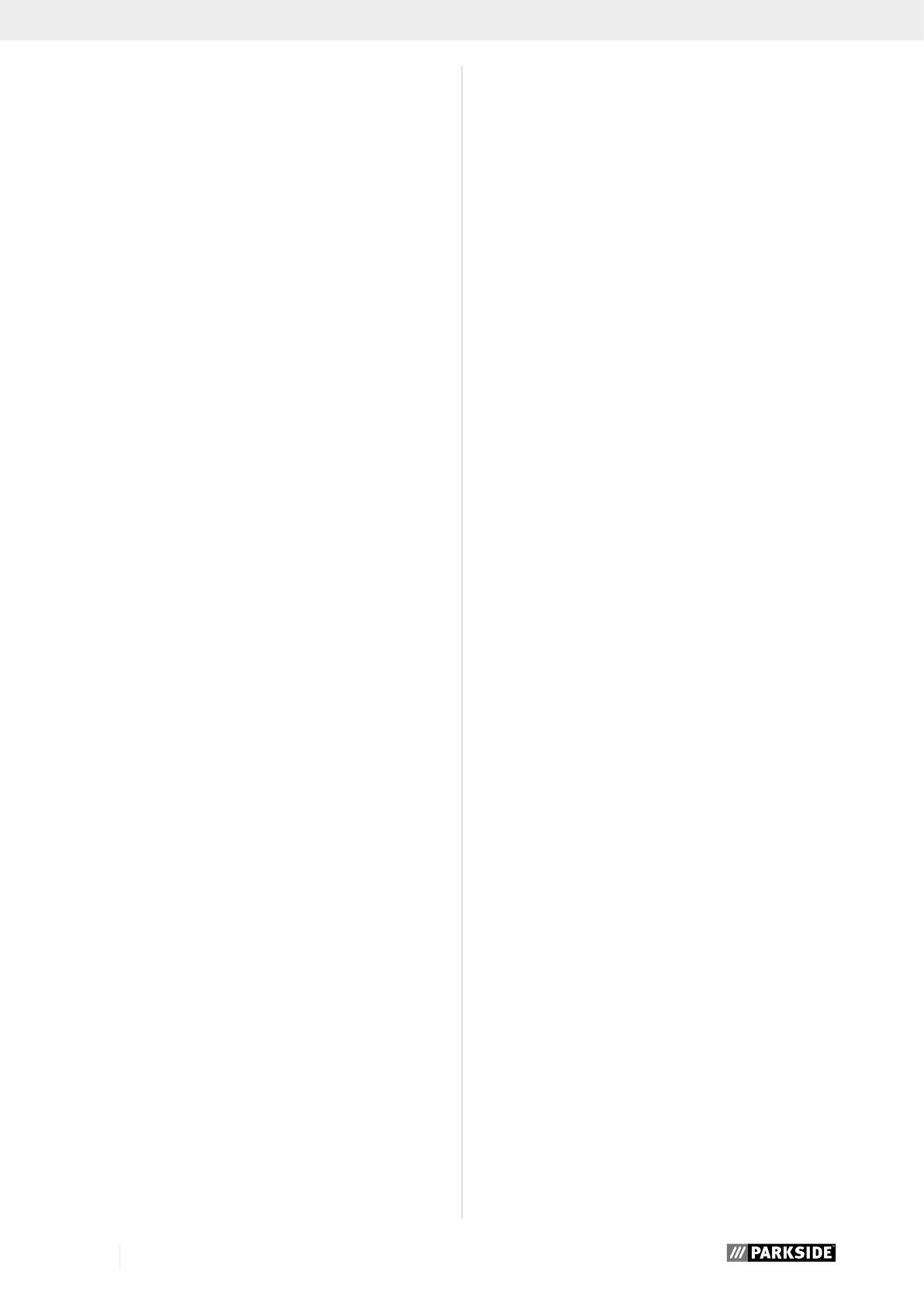
6 GB/CY
d) Make sure the saw blade is not contacting the
guard, riving knife or the workpiece before the
switch is turned on. Inadvertent contact of these items
with the saw blade could cause a hazardous condition.
e) Adjust the riving knife as described in this in-
struction manual. Incorrect spacing, positioning and
alignment can make the riving knife ineffective in reducing
the likelihood of kickback.
f) For the riving knife to work, they must be en-
gaged in the workpiece. The riving knife are inef-
fective when cutting workpieces that are too short to be
engaged with the riving knife. Under these conditions a
kickback cannot be prevented by the riving knife.
g) Use the appropriate saw blade for the riving
knife. For the riving knife to function properly, the saw
blade diameter must match the appropriate riving knife
and the body of the saw blade must be thinner than the
thickness of the riving knife and the cutting width of the saw
blade must be wider than the thickness of the riving knife.
Safety information for sawing
a) m DANGER: Do not place your hands and fin-
gers in the sawing area or close to the saw
blade.
A moment of carelessness or a slip could steer your hand
towards the saw blade and result in serious injuries.
b) Only guide the workpiece against the rotational
direction of the saw blade or cutting tool. Guid-
ing the workpiece in the same direction as the rotational
direction of the saw blade above the table can lead to the
workpiece and your hand being drawn into the saw blade.
c) When performing longitudinal cuts, never use
the mitre stop to guide the workpiece, and
when transverse cutting with the mitre stop
never additionally use the parallel stop for
longitudinal adjustment. Simultaneously guiding the
workpiece with the parallel stop and mitre stop increases
the probability that the saw blade will jam and kickback
will result.
d) When performing longitudinal cuts, always ap-
ply the feed force to the workpiece between
the stop rail and the saw blade. Use a push rod
if the distance between the stop rail and saw
blade is less than 150 mm, and a push block if
the distance is less than 50 mm. This type of work-
ing aid ensures that your hands remain a safe distance
from the saw blade.
e) Only use the push rod provided by the manu-
facturer, or a push rod that has been produced
in accordance with instructions. The push rod
ensures a sufficient distance between the hand and saw
blade.
f) Never use a damaged or partially sawn push
rod. A damaged push rod may break and lead to your
hand running into the saw blade.
g) Never work “freehand”. Always use the paral-
lel stop or the mitre stop to position and guide
the workpiece. “Freehand” means supporting
or guiding the workpiece with the hands, rath-
er than using the parallel stop or mitre stop.
Free-handed sawing leads to incorrect alignment, jamming
and kickback.
h) Never reach around or over a turning saw
blade. Reaching for a workpiece can lead to accidental
contact with the rotating saw blade.
i) Support long and/or wide workpieces at the
rear and/or side of the saw table, so that they
remain horizontal. Long and/or wide workpieces
tend to tilt at the edge of the saw table; this leads to a loss
of control, jamming of the saw blade and kickback.
j) Guide the workpiece steadily and evenly. Do
not bend or twist the workpiece. If the saw
blade jams, switch off the electric tool immedi-
ately, unplug the mains plug and remedy the
cause of the jam. If the saw blade is jammed by the
workpiece, this can lead to kickback or block the motor.
k) Do not remove partially sawn material whilst
the saw is running. Partially sawn material can stick
between the saw blade and stop rail or in the protective
cover, and may draw your fingers into the saw blade during
removal. Switch the saw off and wait until the saw blade
has come to a standstill, before removing the material.
l) For longitudinal cuts on workpieces that are
thinner than 2 mm, use an additional parallel
stop that is in contact with the table surface. Thin
workpieces can wedge under the parallel stop and lead
to kickback.
Kickback - causes and corresponding safety in-
structions
Kickback is a sudden reaction of the workpiece to a catching
or jamming saw blade, or a cut created in the workpiece at an
angle to the saw blade, or if part of the workpiece becomes
jammed between the saw blade and the parallel stop, or an-
other stationary object.
In the majority of cases, with kickback the workpiece is caught
by the rear part of the saw blade, lifted off the saw table and
thrust in the direction of the operator. Kickback is the result of
incorrect or deficient use of the circular table saw. It can be
prevented by suitable precautionary measures, as described
in the following.
a) Never stand directly in line with the saw blade.
Always stand at the side of the saw blade on
which the stop rail is located. With kickback, the
workpiece may be thrust at high speed towards those per-
sons who stand in front of, or in line with the saw blade.
b) Never reach over or behind the saw blade to
pull or support the workpiece. This can result in ac-
cidental contact with the saw blade, or kickback can lead
to your fingers being drawn into the saw blade.
c) Never hold and push the workpiece against
the turning saw blade during sawing. Pushing the
workpiece against the saw blade during sawing will lead
to jamming and kickback.
d) Align the stop rail parallel to the saw blade.
A stop rail that is not aligned will push the workpiece
against the saw blade and create kickback.