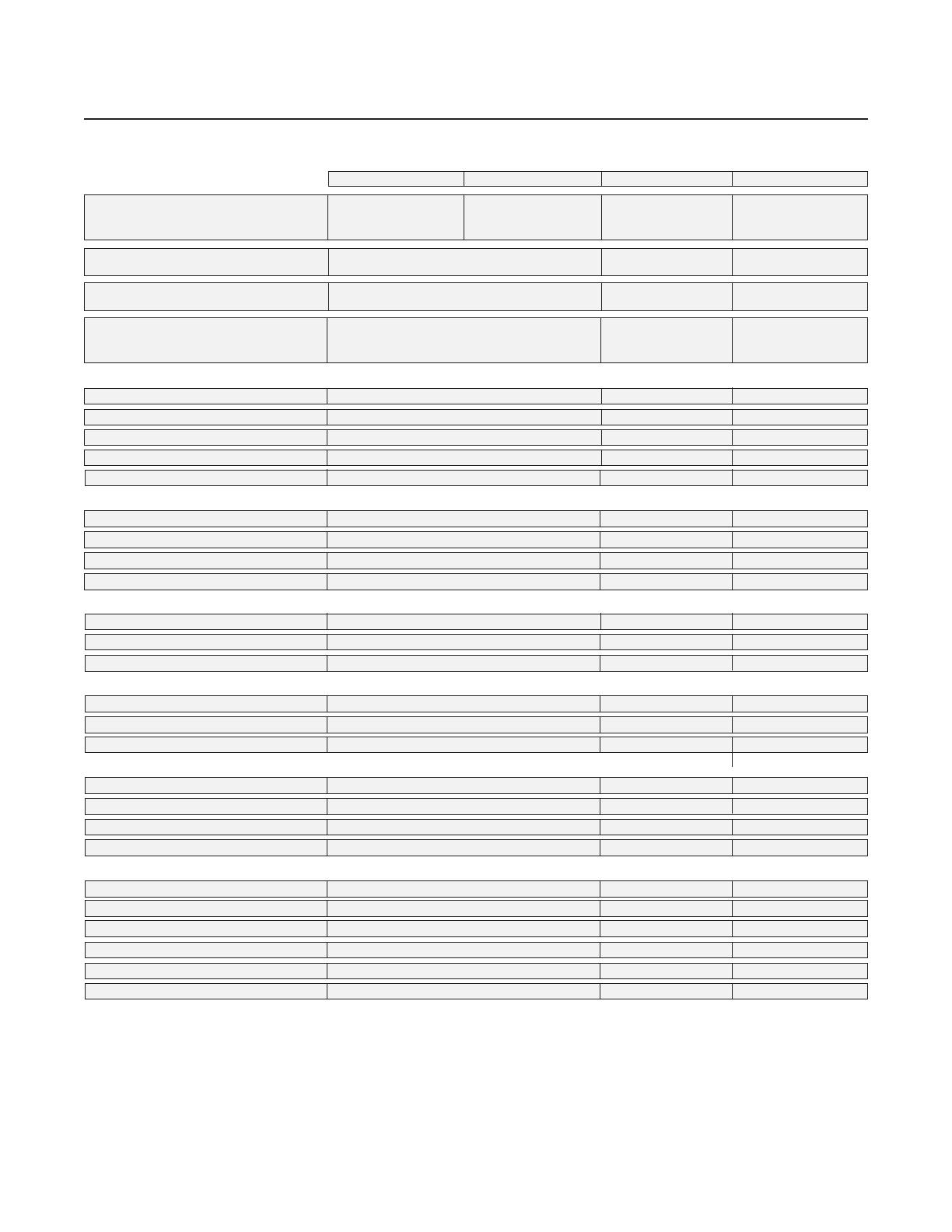
1-4
Brooks
®
Digital MFC's & MFM's
Section 1 Introduction
Installation and Operation Manual
X-TMF-SLA5800-Series-RevB-MFC-eng
Part Number: 541B187AAG
January, 2017
Table 1-2 SLA5800 Series Electrical Specifications
Communication ProtocolCommunication Protocol
Communication ProtocolCommunication Protocol
Communication Protocol
RS485RS485
RS485RS485
RS485
ProfibusProfibus
ProfibusProfibus
Profibus
®®
®®
®
DeviceNetDeviceNet
DeviceNetDeviceNet
DeviceNet
TMTM
TMTM
TM
EtherCATEtherCAT
EtherCATEtherCAT
EtherCAT
®®
®®
®
Electrical ConnectionElectrical Connection
Electrical ConnectionElectrical Connection
Electrical Connection 1 x 15-pin Male Sub-D, 1 x 15-pin Male Sub-D/ 1 x M12 with 5-pin M8 with
(A) 1 x 9-pin Female threaded coupling nut threaded coupling nut
Sub-D (B) 2 x RJ45
Analog I/OAnalog I/O
Analog I/OAnalog I/O
Analog I/O 0-5 V, 1-5 V, 0-10 V, N/A 0-5V
0-20 mA, 4-20 mA
Power Max./PurgePower Max./Purge
Power Max./PurgePower Max./Purge
Power Max./Purge From +13.5 Vdc to From +11 Vdc to From +13.5 Vdc to
+27 Vdc +25 Vdc +27 Vdc
Power Requirements Watts, Max.Power Requirements Watts, Max.
Power Requirements Watts, Max.Power Requirements Watts, Max.
Power Requirements Watts, Max. Valve Orifice > 0.032”: 8 W Valve Orifice > 0.032”: 10 W Valve Orifice > 0.032”: 8.5 W
Valve Orifice ≤ 0.032”: 5 W Valve Orifice ≤ 0.032”: 7 W Valve Orifice ≤ 0.032”: 5.5 W
Without Valve: 2 W Without Valve: 4 W Without Valve: 2.5 W
Voltage Set Point Input SpecificationsVoltage Set Point Input Specifications
Voltage Set Point Input SpecificationsVoltage Set Point Input Specifications
Voltage Set Point Input Specifications
Nominal RangeNominal Range
Nominal RangeNominal Range
Nominal Range 0-5 Vdc, 1-5 Vdc or 0-10 Vdc N/A N/A
Full RangeFull Range
Full RangeFull Range
Full Range (-0.5)-11 Vdc N/A N/A
Absolute Max.Absolute Max.
Absolute Max.Absolute Max.
Absolute Max. 18 V (without damage) N/A N/A
Input ImpedenceInput Impedence
Input ImpedenceInput Impedence
Input Impedence >990 kOhms N/A N/A
Required Max. Sink CurrentRequired Max. Sink Current
Required Max. Sink CurrentRequired Max. Sink Current
Required Max. Sink Current 0.002 mA N/A N/A
Current Set Point Input SpecificationsCurrent Set Point Input Specifications
Current Set Point Input SpecificationsCurrent Set Point Input Specifications
Current Set Point Input Specifications
Nominal RangeNominal Range
Nominal RangeNominal Range
Nominal Range 4-20 mA or 0-20 mA N/A N/A
Full RangeFull Range
Full RangeFull Range
Full Range 0-22 mA N/A N/A
Absolute Max.Absolute Max.
Absolute Max.Absolute Max.
Absolute Max. 24 mA (without damage) N/A N/A
Input ImpedenceInput Impedence
Input ImpedenceInput Impedence
Input Impedence 100 Ohms N/A N/A
Flow Output (Voltage) SpecificationsFlow Output (Voltage) Specifications
Flow Output (Voltage) Specifications
Flow Output (Voltage) Specifications
Flow Output (Voltage) Specifications
Nominal RangeNominal Range
Nominal RangeNominal Range
Nominal Range 0-5 Vdc, 1-5 Vdc or 0-10 Vdc N/A N/A
Full RangeFull Range
Full RangeFull Range
Full Range (-1)-11 Vdc N/A N/A
Min Load ResistanceMin Load Resistance
Min Load ResistanceMin Load Resistance
Min Load Resistance 2 kOhms N/A N/A
Flow Output (Current) SpecificationsFlow Output (Current) Specifications
Flow Output (Current) SpecificationsFlow Output (Current) Specifications
Flow Output (Current) Specifications
Nominal RangeNominal Range
Nominal RangeNominal Range
Nominal Range 0-20 mA or 4-20 mA N/A N/A
Full RangeFull Range
Full RangeFull Range
Full Range 0-22 mA (@ 0-20 mA); 3.8-22 mA (@ 4-20 mA) N/A N/A
Max. LoadMax. Load
Max. LoadMax. Load
Max. Load 380 Ohms (for supply voltage: < 16 Vdc) N/A N/A
Analog I/O Alarm Ouput*Analog I/O Alarm Ouput*
Analog I/O Alarm Ouput*Analog I/O Alarm Ouput*
Analog I/O Alarm Ouput*
TypeType
TypeType
Type Open Collector N/A N/A
Max. Closed (On) CurrentMax. Closed (On) Current
Max. Closed (On) CurrentMax. Closed (On) Current
Max. Closed (On) Current 25 mA N/A N/A
Max. Open (Off) LeakageMax. Open (Off) Leakage
Max. Open (Off) LeakageMax. Open (Off) Leakage
Max. Open (Off) Leakage 1μA N/A N/A
Max. Open (Off) VoltageMax. Open (Off) Voltage
Max. Open (Off) VoltageMax. Open (Off) Voltage
Max. Open (Off) Voltage 30 Vdc N/A N/A
Analog I/O Valve Override Signal Specifications**Analog I/O Valve Override Signal Specifications**
Analog I/O Valve Override Signal Specifications**Analog I/O Valve Override Signal Specifications**
Analog I/O Valve Override Signal Specifications**
Floating/UnconnectedFloating/Unconnected
Floating/UnconnectedFloating/Unconnected
Floating/Unconnected Instrument controls valve to command set point N/A N/A
VOR < 0.3 VdcVOR < 0.3 Vdc
VOR < 0.3 VdcVOR < 0.3 Vdc
VOR < 0.3 Vdc Valve Closed N/A N/A
1 Vdc < VOR < 4 Vdc1 Vdc < VOR < 4 Vdc
1 Vdc < VOR < 4 Vdc1 Vdc < VOR < 4 Vdc
1 Vdc < VOR < 4 Vdc Valve Normal N/A N/A
VOR > 4.8 VdcVOR > 4.8 Vdc
VOR > 4.8 VdcVOR > 4.8 Vdc
VOR > 4.8 Vdc Valve Open N/A N/A
Input Impedence
Input Impedence
Input ImpedenceInput Impedence
Input Impedence 800 kOhms N/A N/A
Absolute Max. InputAbsolute Max. Input
Absolute Max. InputAbsolute Max. Input
Absolute Max. Input
(-25 Vdc) < VOR < 25 Vdc (without damage) N/A N/A
*The Alarm Output is an open collector or "contact type" that is CLOSED (on) whenever an alarm is active.
The Alarm Output may be set to indicate any one of various alarm conditions.
** The Valve Override Signal (VOR) is implemented as an analog input which measures the voltage at the input and controls the
valve based upon the measured reading as shown in this section.