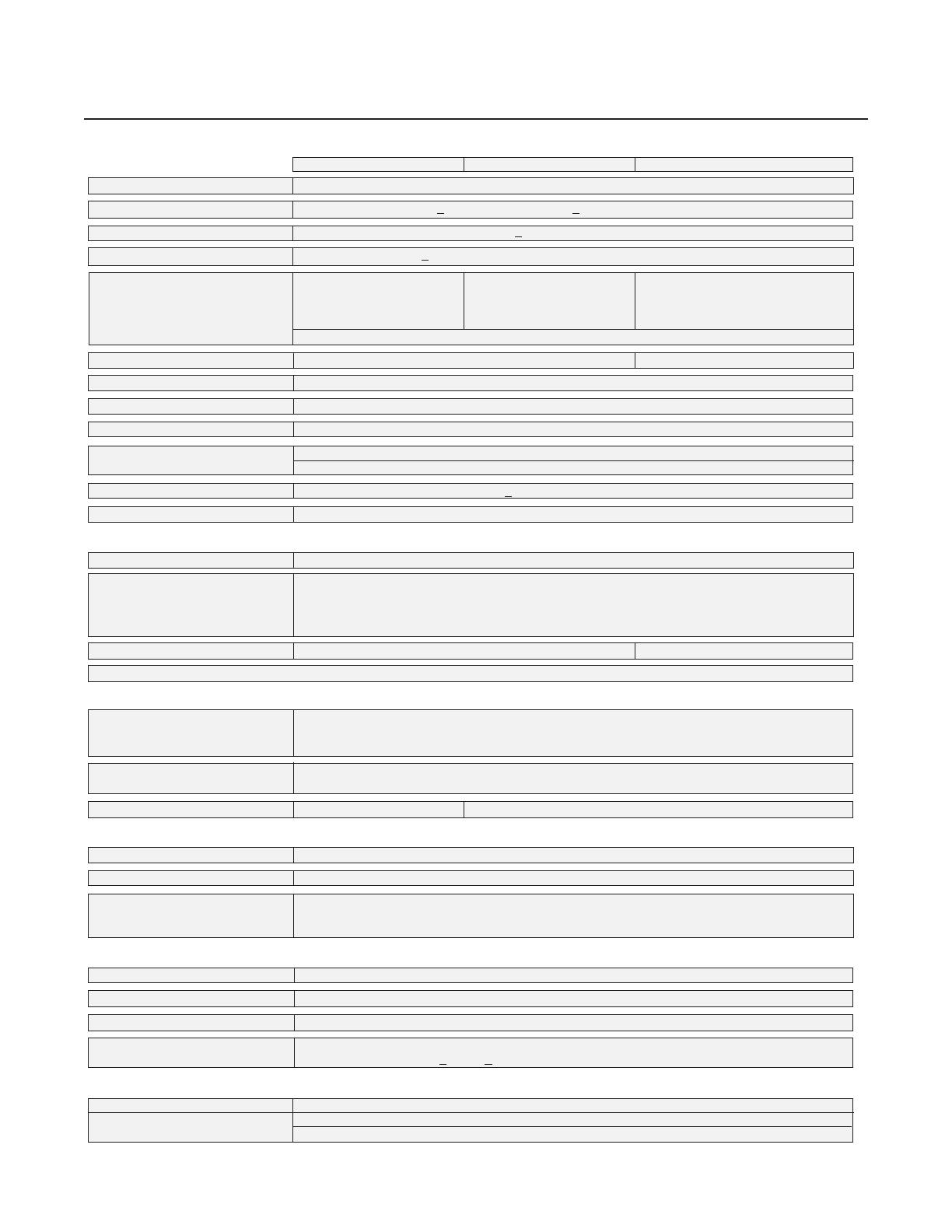
1-9
GF100 Series
Installation and Operation Manual
X-TMF-GF100-Series-MFC-eng
Part Number: 541B137AAG
April, 2017
Section 1 Introduction
Table 1-3 Specifications for Standard GF100/GF120/GF125 Series
GF100GF100
GF100GF100
GF100
GF120GF120
GF120GF120
GF120
GF125GF125
GF125GF125
GF125
Electrical Electrical
Electrical Electrical
Electrical
Electrical Connection Electrical Connection
Electrical Connection Electrical Connection
Electrical Connection RS485/Analog via 9-Pin “D” connector, DeviceNet
TM
via 5-Pin “M12” connector
Digital Communication Digital Communication
Digital Communication Digital Communication
Digital Communication RS485+ (model specific), DeviceNet (model specific), RS485 Diagnostic Port (all models)
Diagnostic /Service Port Diagnostic /Service Port
Diagnostic /Service Port Diagnostic /Service Port
Diagnostic /Service Port RS485 via 2.5mm jack
Power Supply/Consumption Power Supply/Consumption
Power Supply/Consumption Power Supply/Consumption
Power Supply/Consumption DeviceNet: 545mA max. @ +11-25 Vdc., 250mA max. @ 24Vdc
RS485/Analog: 6 Watts max @
+15Vdc. (+10%) or +24 Vdc (±10%)
PerformancePerformance
PerformancePerformance
Performance
Full Scale Flow Range (NFull Scale Flow Range (N
Full Scale Flow Range (NFull Scale Flow Range (N
Full Scale Flow Range (N
22
22
2
Eq.) Eq.)
Eq.) Eq.)
Eq.) 3 sccm to 55 slm
Flow AccuracyFlow Accuracy
Flow AccuracyFlow Accuracy
Flow Accuracy
+1% S.P. > 35-100%, +0.35% F.S. 2-35%
Repeatability & ReproducibilityRepeatability & Reproducibility
Repeatability & ReproducibilityRepeatability & Reproducibility
Repeatability & Reproducibility <
+ 0.15% S.P.
LinearityLinearity
LinearityLinearity
Linearity
+ 0.5% F.S. (included in accuracy)
Response Time (Settling Time)Response Time (Settling Time)
Response Time (Settling Time)Response Time (Settling Time)
Response Time (Settling Time) 300ms (3-860 sccm N2 Eq.)
Normally Closed ValveNormally Closed Valve
Normally Closed ValveNormally Closed Valve
Normally Closed Valve < 1 sec 700ms 400ms (861-7200 sccm N2 Eq.)
500ms (7201-30000 sccm N2 Eq.)
<700ms (30001-55000 sccm N2 Eq.)
Normally Open ValveNormally Open Valve
Normally Open ValveNormally Open Valve
Normally Open Valve <1.5 sec
Pressure InsensitivityPressure Insensitivity
Pressure InsensitivityPressure Insensitivity
Pressure Insensitivity Not Applicable
< 5% SP up to 5 psi/sec upstream press. spike
Control RangeControl Range
Control RangeControl Range
Control Range 2-100% (Normally Closed Valve) 3-100% (Normally Open Valve)
MultiFloMultiFlo
MultiFloMultiFlo
MultiFlo
standard
#of Bins#of Bins
#of Bins#of Bins
#of Bins 11 bins
Valve Shut Down (N.C. Valve)Valve Shut Down (N.C. Valve)
Valve Shut Down (N.C. Valve)Valve Shut Down (N.C. Valve)
Valve Shut Down (N.C. Valve) < 1% of F.S.
Valve Shut Down (N.O. Valve)Valve Shut Down (N.O. Valve)
Valve Shut Down (N.O. Valve)Valve Shut Down (N.O. Valve)
Valve Shut Down (N.O. Valve) 2% of F.S.
Zero StabilityZero Stability
Zero StabilityZero Stability
Zero Stability <
+ 0.5% F.S. per year
Temperature CoefficientTemperature Coefficient
Temperature CoefficientTemperature Coefficient
Temperature Coefficient Span: 0.05% S.P. per
o
C, Zero: 0.005% F.S. per
o
C
RatingsRatings
RatingsRatings
Ratings
Operating Temperature RangeOperating Temperature Range
Operating Temperature RangeOperating Temperature Range
Operating Temperature Range
10-50
o
C
Differential Pressure Range*Differential Pressure Range*
Differential Pressure Range*Differential Pressure Range*
Differential Pressure Range* 3-860 sccm = 7-45 psid, 861- 7200 sccm = 10-45 psid, 7201-55000 sccm = 15-45 psid
*Argon gas applications require an additional 10 psid differential pressure.
Low vapor pressure gases require an inlet pressure of > 100 Torr, with vacuum on outlet
(example SiCl4). Contact Brooks Technical Support for more information.
Maximum Operating PressureMaximum Operating Pressure
Maximum Operating PressureMaximum Operating Pressure
Maximum Operating Pressure
500 psia max 100 psia max
Leak Integrity (external)Leak Integrity (external)
Leak Integrity (external)Leak Integrity (external)
Leak Integrity (external)
1x10
-10
atm. cc/sec He
Compliance Compliance
Compliance Compliance
Compliance
EMCEMC
EMCEMC
EMC EC Directive 2004/108/EC CE: EN61326: 2006 (FCC Part 15 & Canada IC-subset of CE testing)
Environmental ComplianceEnvironmental Compliance
Environmental ComplianceEnvironmental Compliance
Environmental Compliance RoHS Directive (2011/65/EU)
REACH Directive EC 1907/2006
NOTE: See the following Safe Delivery System (SDS) section for optional detailed specifications
Diagnostics & DisplayDiagnostics & Display
Diagnostics & DisplayDiagnostics & Display
Diagnostics & Display
Status LightsStatus Lights
Status LightsStatus Lights
Status Lights MFC Health, Network Status
AlarmsAlarms
AlarmsAlarms
Alarms
Control Valve Output, Network Interruption
Display TypeDisplay Type
Display TypeDisplay Type
Display Type Top Mount Integrated LCD
Viewing Angle / Viewing DistanceViewing Angle / Viewing Distance
Viewing Angle / Viewing DistanceViewing Angle / Viewing Distance
Viewing Angle / Viewing Distance Fixed /
10 feet
Units Displayed / ResolutionUnits Displayed / Resolution
Units Displayed / ResolutionUnits Displayed / Resolution
Units Displayed / Resolution Flow (%), Temp. (
o
C), Pressure (psia, kPa) /
0.1 (unit)
MechanicalMechanical
MechanicalMechanical
Mechanical
Valve TypeValve Type
Valve TypeValve Type
Valve Type Normally Closed
Normally Open
Meter (no valve)
Wetted MaterialsWetted Materials
Wetted MaterialsWetted Materials
Wetted Materials GF100: SEMI F20 HP Compliant, 316L VIM/VAR, Hastelloy C-22, 316L Stainless Steel, 304 Stainless Steel, KM-45
GF120/GF125: SEMI F20 UHP Compliant, 316L VIM/VAR, Hastelloy C-22, 316L Stainless Steel, 304 Stainless Steel, KM-45
Surface FinishSurface Finish
Surface FinishSurface Finish
Surface Finish 10μ inch Ra 4μ inch Ra (0.1 μm Ra)