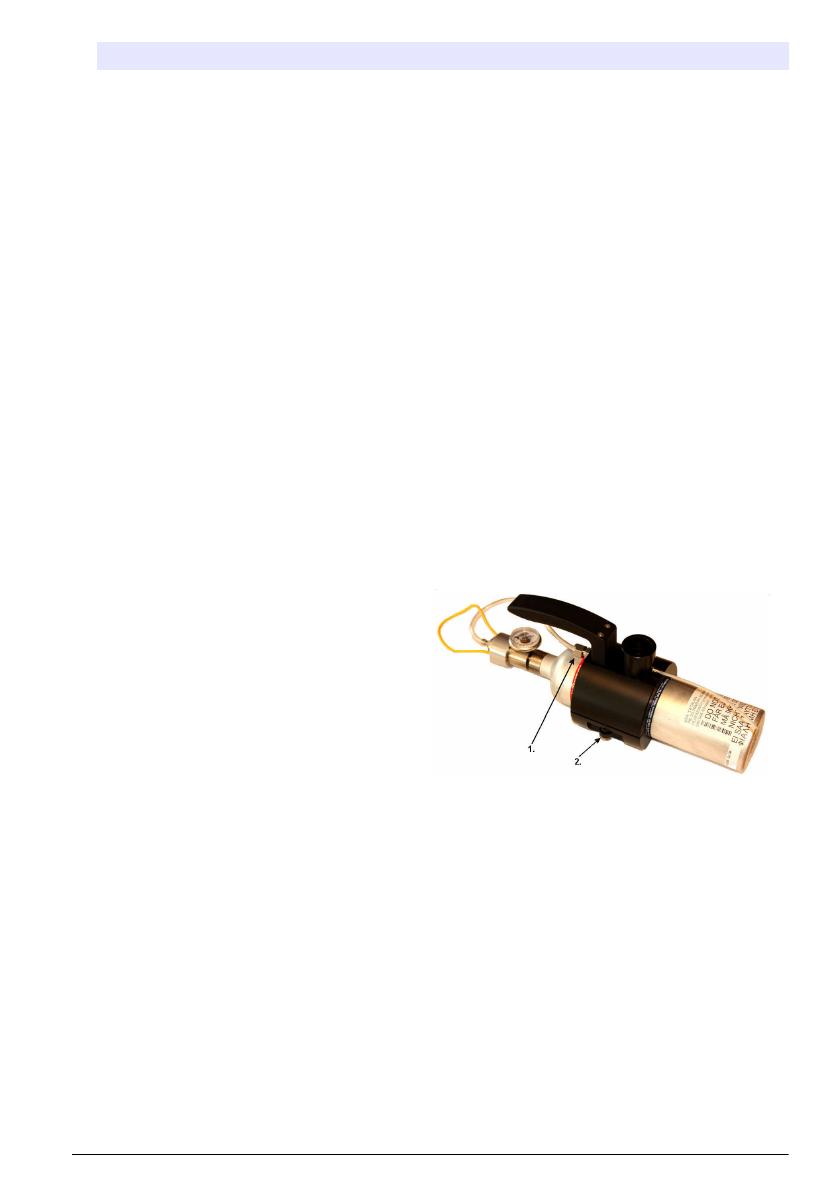
Option Description
FLASH time The delay between two data file transfers from volatile memory into non-volatile
memory. The last data file erases the previous one. This option is only available if
the Auto save in flash box is checked.
Save in flash now Press this button to store measurement data in flash immediately. After pressing
this button, press OK to initiate the process. A warning screen appears informing
you that the operation can take up to 30 seconds. Press Yes to continue or No to
abort.
Auto save in flash Check this box to save measurements in flash automatically. Measurements are
saved at regular time intervals as defined in the FLASH time box.
Purge data Clear all data in the volatile and non-volatile memories.
Start logging
measurements
Only available in Store once mode, this option starts or stops the measurement
recording session. Measurement recording ends automatically when the buffer is
full.
Open data Opens a table showing the measurments stored in the volatile memory (RAM).
Note: If TPO or TPA calculation is enabled, a ”TPO data” or a ”TPA data” button will
be available underneath the “Open data” button described above. Pressing this
button will display the TPO or TPA calculated data in a screen similar to that for
standard data.
Calibration
Calibrations can only be performed once the instrument has been installed and configured.
Note: The temperature sensor is factory calibrated and can only be changed by a Hach representative.
Portable calibration device
The portable calibration device (part number 33088)
is ideal for calibrating the sensor close to its location
in the sample. The device is designed to hold a one
liter gas cylinder but is fully compatible for use with
other kinds of gas cylinders.
When using other types of gas cylinders, simply
connect the gas supply to the Swagelok connector
(No. 1), and make sure that the inlet gas pressure
does not exceed 2 bars absolute.
The gas bottle is not supplied and must be
purchased locally.
To ensure the calibration works correctly the calibration gas bottles must be of 99.999% (50) quality
or better. Bottles containing 34 liters of compressed gas with a 5/8-18 UNF (C10) fitting are
compatible with the hand-held calibration device and recommended for this purpose. Empty gas
bottles are easily removed from the device. Simply unscrew the small screw (No. 2) a few turns, slide
the bottle out of the holder, and unscrew the bottle from the pressure reducer. Follow this same
procedure in reverse order to install a new bottle.
Sensor calibration
The sensor can be calibrated manually on an ad hoc basis. By default, the mode is set to zero
calibration with auto-end.
For higher level concentrations (above 1% oxygen which corresponds to about 400 ppb dissolved
O
2
) a high level adjustment can be performed using a gas mixture containing more than 1% oxygen,
or a known line sample. However, this should not be done without first ensuring the zero point is
accurate. This can be achieved by performing a zero calibration first.
Low range sensors: (K1200-L spots)
English
19