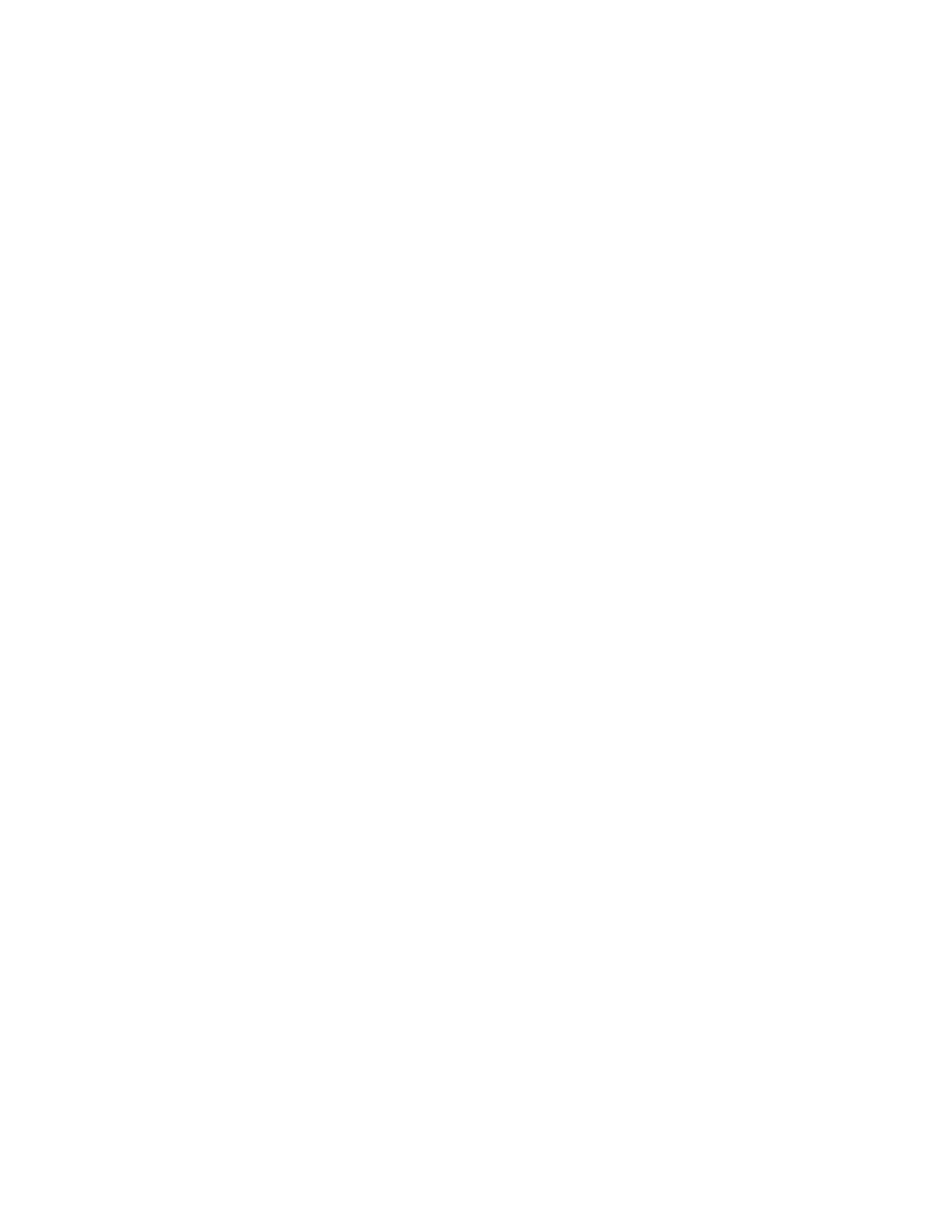
4
1.0 APPLICATIONS
When used in combination with the Lad-Saf™ Detachable Cable Sleeve (sold separately), the Lad-Saf™
Flexible Cable Ladder Safety System (Figure 1) is designed to protect a worker in the event of a fall while climbing xed
ladders or similar climbing structures. LAD-SAF
™
systems are intended to be installed on xed ladders or ladder like
climbing surfaces that are part of a structure (e.g., water tank ladders, mono poles [wood, steel, or concrete] buildings,
manways, antenna structures and towers).
LAD-SAF
™
systems are not intended to be installed on portable ladders. These systems are designed
for use on ladders that are generally vertical. The ladder safety system must not exceed a maximum angle of 15° from
vertical. The following application limitations must be considered before installing the LAD-SAF
™
system.
The ladder structure to which the system is installed must be capable of withstanding the
loads applied by the system in the event of a fall (see Section 2.2).
The number of users allowed on the system at one time varies depending on the type of
system and installation. Generally, system capacities range from one to four users. See sections 2.0 and 3.0 for more
information on capacity limitations. System capacities are based on a maximum user weight, including tools and
clothing, of 310 lbs (140.6 kg).
Use of this equipment in areas with environmental hazards may require that
additional precautions be taken to reduce the possibility of injury to the user or damage to the equipment. (e.g., high
heat caused by welding or metal cutting, caustic chemicals, seawater, high voltage power lines, explosive or toxic
gases, moving machinery, sharp edges).
This equipment is intended to be installed by persons who have been trained in its correct application.
Refer to applicable local, and national requirements governing this equipment for more information on ladder safety
systems and associated components, including OSHA 1910.27.
2.0 SYSTEM REQUIREMENTS
This equipment is designed for use with DBI-SALA approved
components and subsystems. The use of non-approved components and subsystems (e.g., harnesses, lanyards, sleeves,
etc.) may jeopardize compatibility of equipment, and could aect the safety and reliability of the complete system. If you
have questions on the installation or suitability of this equipment for your application, contact DBI-SALA.
The DBI-SALA Lad-Saf™ Ladder Safety Systems, including the DBI-
SALA Lad-Saf™ Detachable Cable Sleeves, are designed for use with DBI-SALA approved climb assist systems. The use of
any other type of climb assist system, including a powered climb assist system, may be incompatible with the Lad-Saf™
Ladder Safety System and Detachable Cable Sleeves, and could create a serious safety hazard for the user. Do not use
non-DBI-SALA climb assist systems without rst consulting a competent person and/or a qualied person at your worksite
for approval. If you have additional questions about compatibility, please contact 3M Technical Services.
The climbing structure to which the
LAD-SAF
™
system is installed must be capable of supporting the loads imposed by the system. For calculation purposes
the required bracket load may be assumed to be distributed evenly between the number of rung attachments. For
example, the TB-3 top bracket (Figure 2) is supplied with three rung connections. The load required for each rung for a
single user system is 1,125 lbs (5.0 kN) per rung (3,375 lbs [15.0 kN]/3).
(See Figure 2 and TB Items Part List) The top bracket connection loads include system pretension
and forces associated with arresting a fall. Load requirements for the top bracket vary depending on the number of
users allowed on the system at one time, top bracket model, and type of connection to the structure.
Item Numbers; TB-2, TB-3, TB-4, TB-6, TB-7, TB-10 and Part Numbers; 6116048, 6116050, 6116051, 6116052,
TB-1, 6116055, 6116057, 6116059, TB-5, 6116282, 6116286, 6116290, 6116291, 6116292, 6116293, 6116294,
6116295, 6116296.
Note: Other installation requirements may limit the number of users allowed on a system. See section 3.0.
Top Bracket Connection Loads:
• One user on the system: 3,375 lbs (15.0 kN)
• Two users on the system: 4,350 lbs (19.3 kN)
• Three users on the system: 5,325 lbs (23.7 kN)
• Four users on the system: 6,300 lbs (28.0 kN)
Exception: TB-1 top bracket is designed for use with 6116336 or 6116337 grab bar extension. When the grab bar is
used as a connection for a personal fall arrest system the bracket connection must support a minimum of 5,000 lbs
(22.2 kN)., or 3,600 lbs (16.0 kN) for a certied anchorage. See ANSI Z359.1 and OSHA regulations.
Item Numbers; TB-8, TB-9, TB-11 and Part Numbers 6116074, 6116325, 6116324 and 6116328.
Exception: TB-9 (6116074) allows two users.
Top Bracket Connection Loads:
• One user on the system: 3,375 lbs (15.0 kN)
• Two users on the system: 4,350 lbs (19.3 kN)
The bottom bracket connection must be capable of supporting a system pretension load of
750 lbs (3.3 kN) in the direction of loading.